The etherification reaction is generally a chemical reaction carried out under acidic catalytic conditions. In the petrochemical industry, processes such as light gasoline etherification and MTBE production currently use resin catalysts (e.g., Southwind) for reaction catalysis, while unreacted methanol is recovered.
However, the introduction of acidic catalysts during the etherification process generates a certain level of acidity in the system. This acidity adversely affects methanol recovery system equipment in domestic etherification units, which are primarily constructed from carbon steel. Corrosion of equipment and pipelines has become a common phenomenon.
If the acidic environment in the system is not controlled in a timely and effective manner, corrosive damage to the methanol recovery system will occur. This typically manifests as sludge covering the trays in the methanol extraction tower, blockage of flow channels, and corrosive sludge buildup in outlet pumps, leading to system shutdown and posing significant safety hazards.
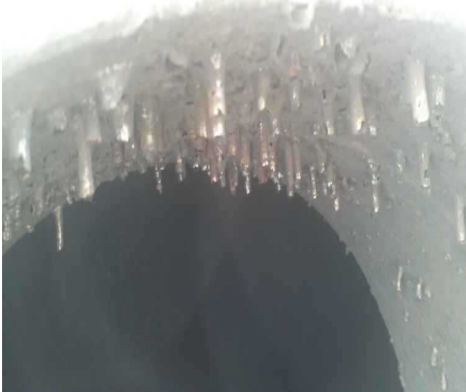
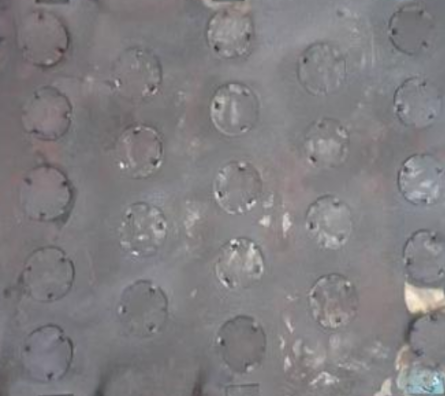
Photos of Corrosion in the Methanol Recovery System
To regulate system acidity, methods such as water replacement and alkali addition are commonly used to increase water pH and reduce system acidity, thereby minimizing corrosion. However, adding alkali can lead to catalyst poisoning in etherification resin catalysts, affecting their performance and lifespan. Many etherification units resort to replacing large amounts of extraction water to control the system’s pH, which causes significant demineralized water wastage and poses environmental challenges.
To address this common industry issue, Southwind has conducted research and analysis of the etherification system feed environment and developed the Seplite® LXC-104 Deacidifier for etherification systems, along with a complete deacidification process package. The process flow diagram is shown below:
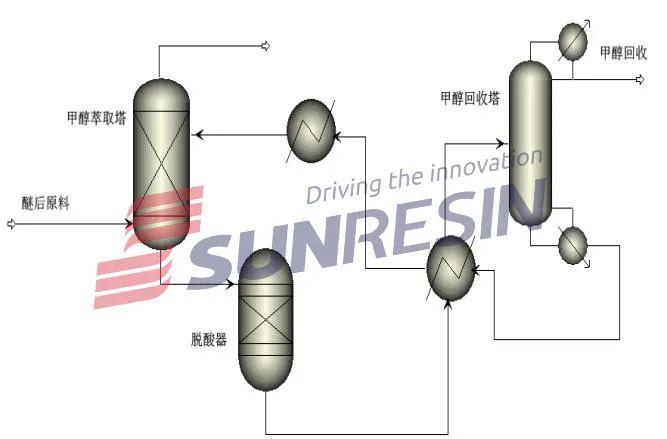
Advantages of Seplite® LXC-104 Deacidifier:
- Strong anti-fouling capability
- High number of strong alkaline functional groups
- Synergistic effects from the introduction of composite groups
These advantages allow for the effective removal of acidic ions, metal ions, and chloride ions from the circulating water in etherification systems. Large-scale industrial application over several years has demonstrated that the circulating water quality can consistently maintain a pH value above 6.5, effectively reducing the risk of corrosion in methanol recovery systems and ensuring more stable and safe system operation.
The Seplite® LXC-104 deacidification system is easy to operate, environmentally friendly, and more economical.
Southwind offers a complete solution to customers, including:
- Deacidifiers
- Deacidification process technology and full system equipment
- Process commissioning and technical guidance