Chlorinated hydrocarbons, such as methylene chloride, ethylene dichloride, and chloroform, are commonly used as solvents or synthetic raw materials in industries like pharmaceuticals, pesticides, and fine chemicals. However, due to their relatively low boiling points, these chlorinated hydrocarbons tend to volatilize significantly during production, causing material loss and creating environmental pressure due to the waste gas emitted in the process.
In dealing with chlorinated hydrocarbon waste gas VOCs, conventional methods such as activated carbon (carbon fiber) adsorption face challenges due to low selectivity in adsorption, leading to low removal and recovery efficiency, with fluctuations in performance that make it difficult to maintain stable outlet emissions. Additionally, activated carbon (carbon fiber) needs to be replaced frequently, generating hazardous waste that adds operational burden for businesses. Therefore, the use of activated carbon (carbon fiber) for handling chlorinated hydrocarbon waste gases is not the most efficient solution. Furthermore, Regenerative Thermal Oxidizer (RTO) technology, which is widely used in VOC waste gas treatment, faces limitations when dealing with chlorinated hydrocarbon gases. Chlorinated hydrocarbons produce corrosive hydrochloric acid gas and carcinogenic dioxins during combustion, restricting RTO use to gases with chlorinated hydrocarbon content below 200 mg/m³.
In response to this challenge, Southwind Technology has innovatively introduced resin adsorption technology for chlorinated hydrocarbon waste gas treatment. The specially designed resin framework achieves high selectivity for chlorinated hydrocarbon molecules through its molecular structure. The complex pore structure inside the resin enables efficient adsorption and interception of chlorinated hydrocarbons in waste gas, followed by resource recovery. Industrial validation shows that Southwind’s dedicated waste gas treatment resins and matching equipment achieve a removal and recovery rate of over 99%, with stable emissions meeting standards. The resin products and technology have been widely recognized by relevant enterprises.
Advantages of Southwind’s Resin and Technology for Chlorinated Hydrocarbon Waste Gas Treatment
High Efficiency and Precision: The resin offers excellent adsorption efficiency, achieving a removal and recovery rate of over 99% for chlorinated hydrocarbon molecules, with high treatment precision and capacity.
Lower Energy Consumption: The resin is composed of regular spherical particles with structural strength, resulting in lower operational air resistance compared to activated carbon (carbon fiber) systems, thus reducing energy consumption.
Stable Performance and Long Lifespan: The treatment indicators remain stable, with minimal resin loss. Under normal conditions, the resin has a lifespan of over five years, and the annual replenishment rate is less than 10%.
Cost-Effective: The treatment cost is significantly lower than that of activated carbon (carbon fiber) adsorption and recovery processes.
High Flexibility: The resin can handle larger air volumes and concentration fluctuations, providing greater operational flexibility.
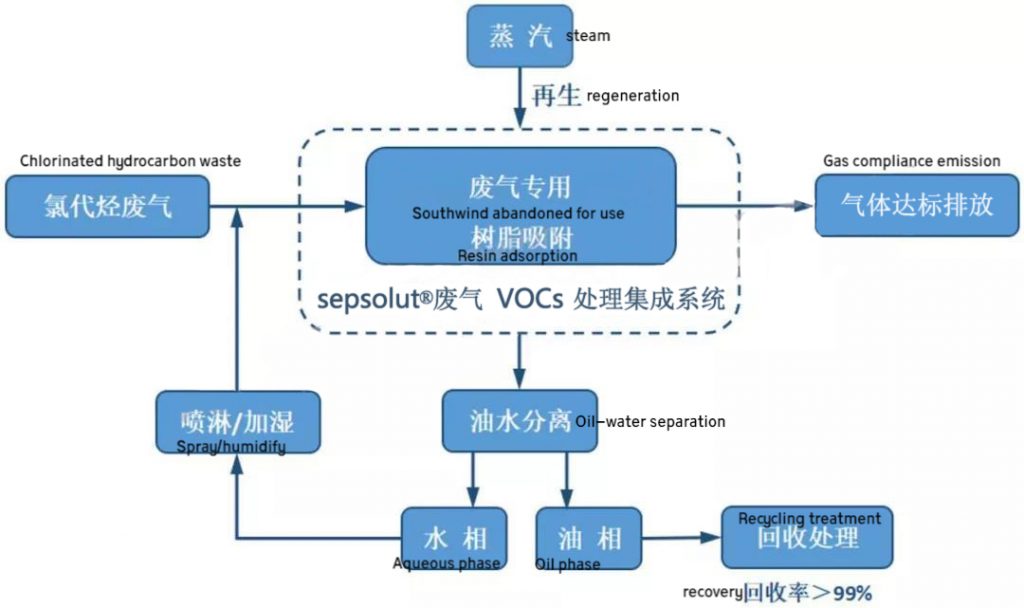